DRIPSTOP® Protection Put To The Test
DRIPSTOP® Protects Metal Panels
FILC, the makers of DRIPSTOP®, tested the product to gauge the benefits of using it in an animal confinement setting. Here’s a summary of the test.
1. Purpose of the Test
The purpose of this test was to research how DRIPSTOP® provides additional protection to the metal roof panels in buildings used for livestock confinement, where corrosion is very likely to occur.
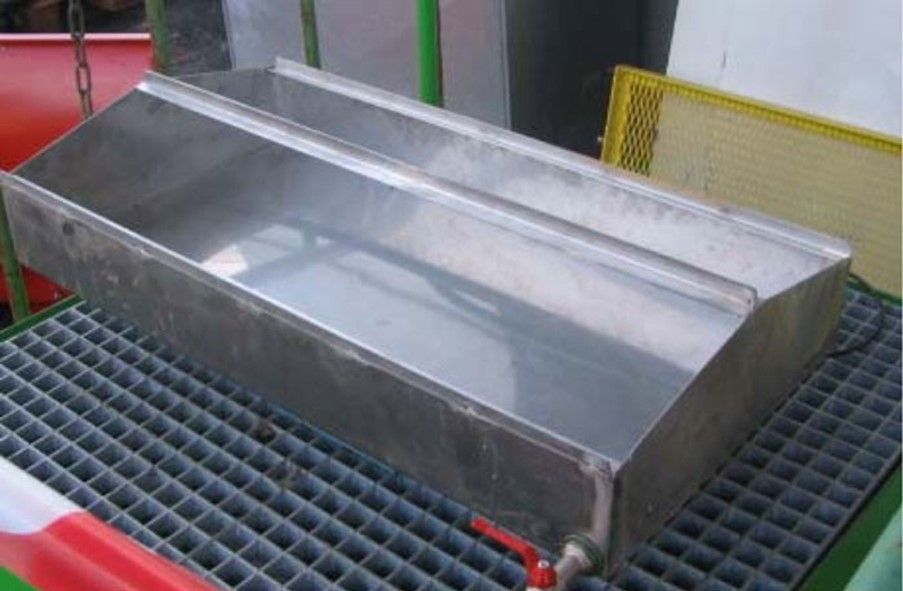
Testing chamber similar to a chafing dish. Images courtesy of DRIPSTOP®/FILC
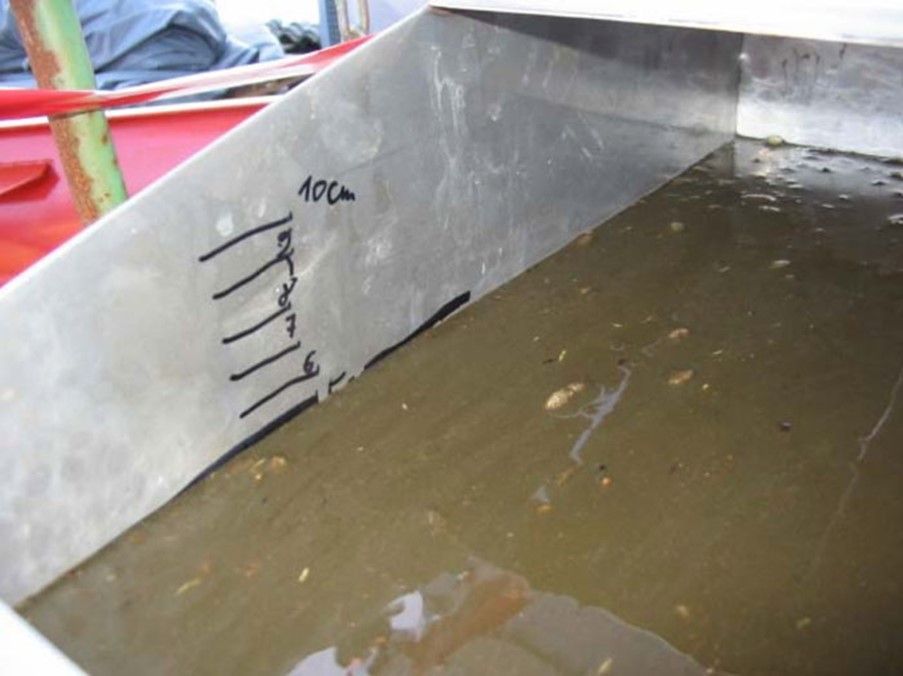
Testing chamber filled with liquid manure.
2. Testing
As there is no standardized test for corrosion in livestock confinement, the first task was to find the most corrosive tests regularly run on steel panels and see if they could be adapted to livestock confinement. In talks with some of the world’s largest steel producers, one test seemed to lend itself well to the need.
The idea of the test was to loosely copy the humidity chamber testing also known as the Cleveland Condensing Test (ASTM-D4584). The test was performed on steel sheets with a protective layer of zinc (galvanized). Instead of the usual water, livestock confinement conditions were simulated in a chamber filled with liquid manure, heated from below.
By heating the liquid manure, the temperature difference between inside and outside the chamber kept humidity levels at close to 100% and left a constant state of condensation on the test panels. Steel sheet test samples with and without DRIPSTOP® were directly exposed to the simulated environment.
We observed the changes on the surface of each metal sheet after 2, 4 and 6 weeks (1000 hours). Samples were compared with original metal sheets, which had not been exposed to the testing conditions.
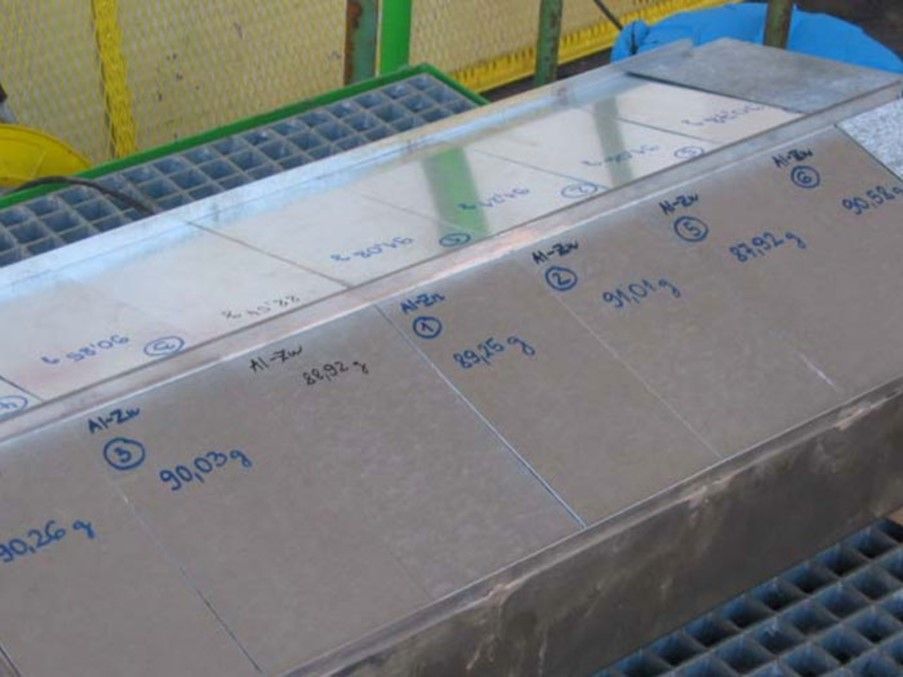
3. Conclusion
This test provides significant evidence that DRIPSTOP® protects metal panels exposed to severe conditions in buildings used for livestock confinement. The panels covered with DRIPSTOP® resist corrosion much better.
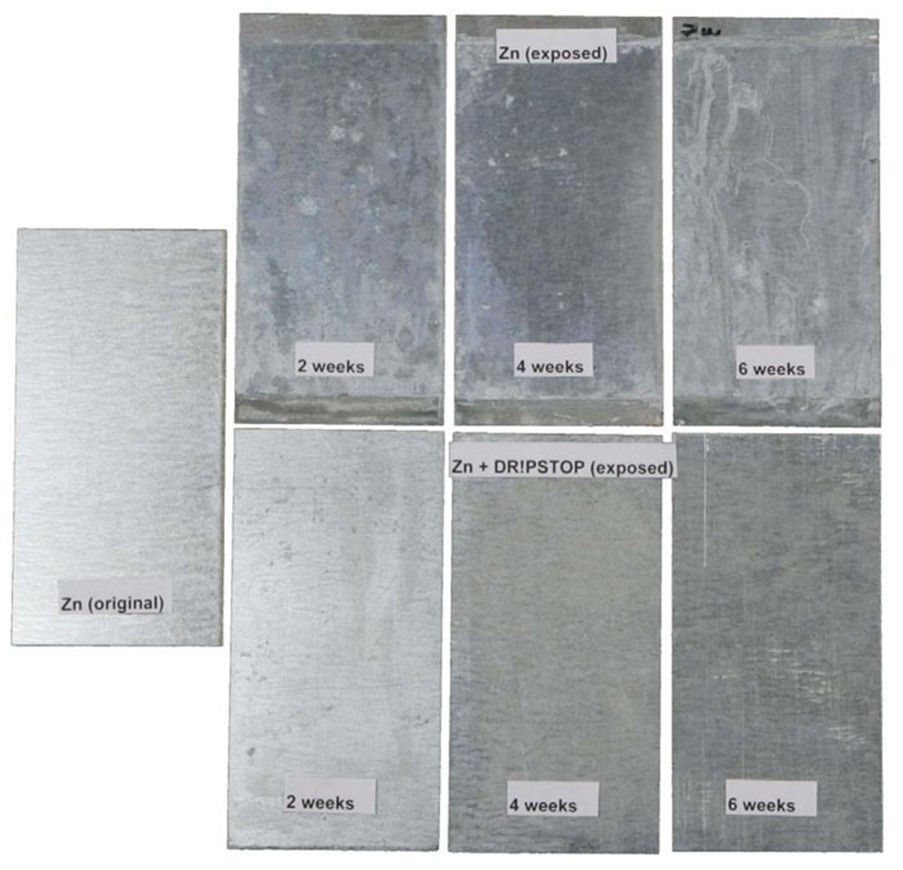
Steel test samples and their protective coating: Galvanized (Zinc Coating: U.S. Steel DX51D, 200g/m2 Zn)
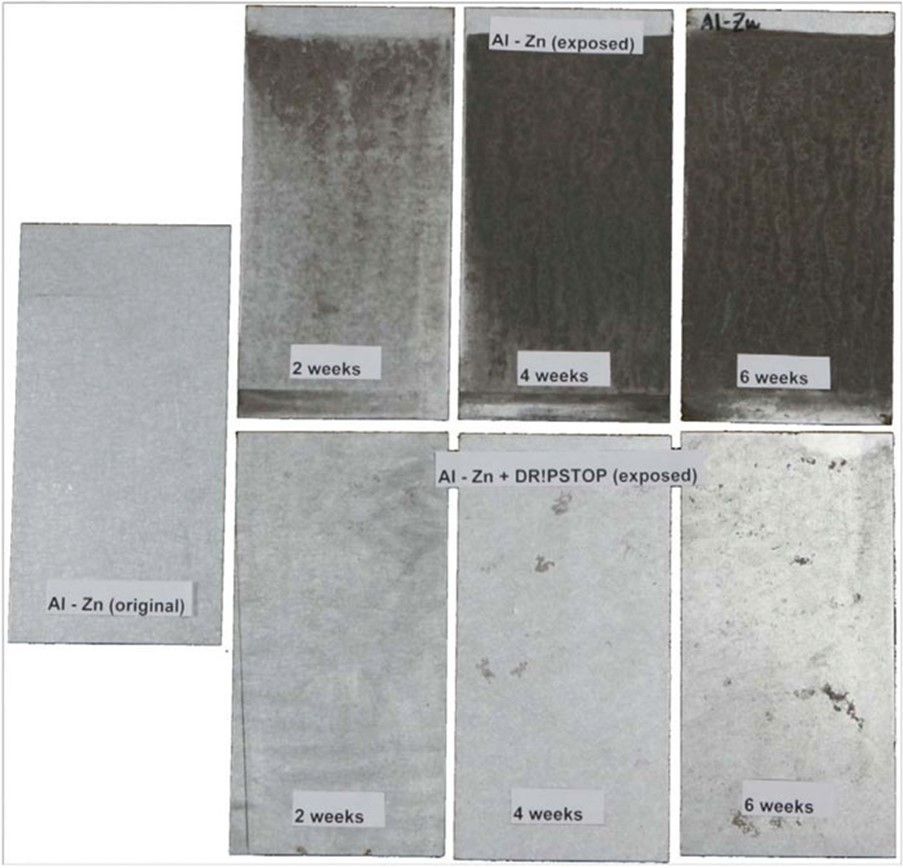
Steel test samples and their protective coating: Galvalume (Zinc + Aluminum coating)
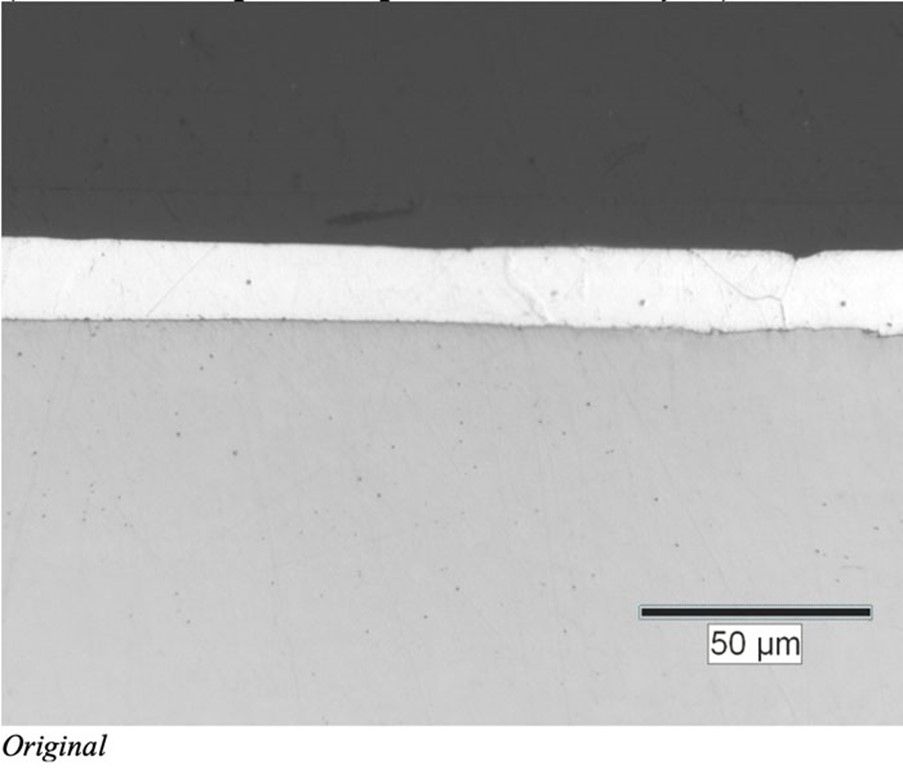
Microscopic cross section analysis (Galvanized, 500 times magnification). The white stripe is the protective zinc layer. Original.
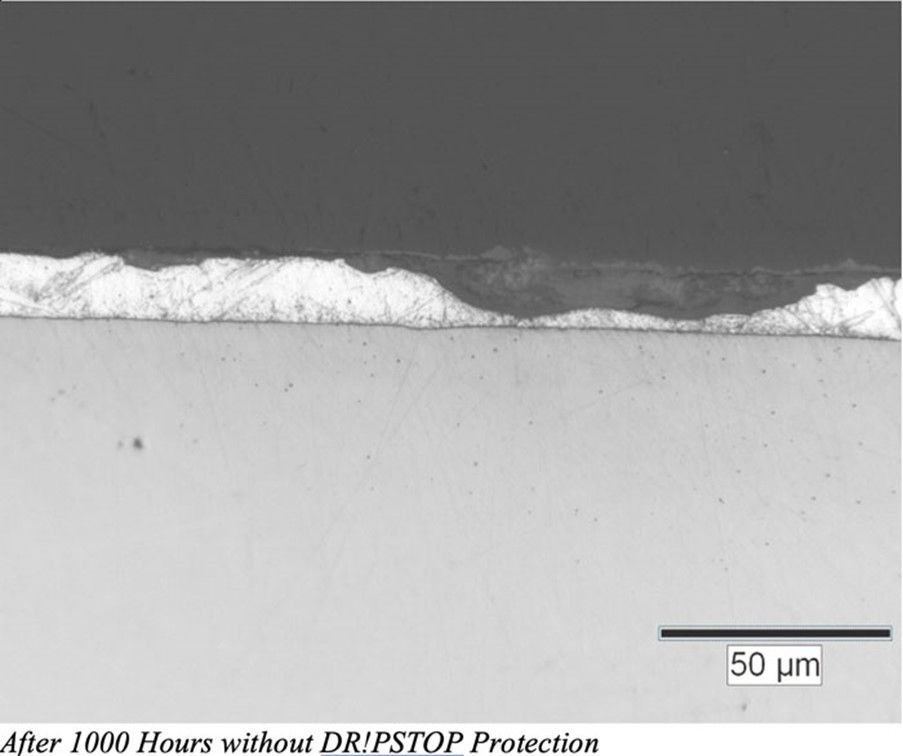
After 1,000 Hours without DRIPSTOP® Protection. Photos courtesy of FILC/DRIPSTOP®
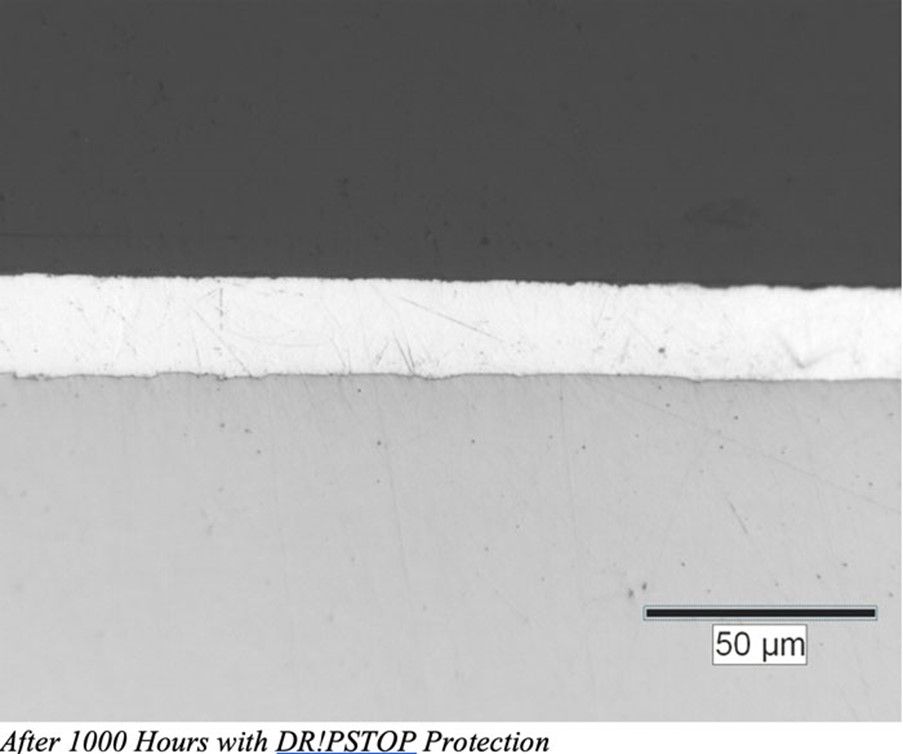
After 1,000 hours WITH DRIPSTOP® protection.
Article was published on website FrameBuildingNews